How to Reduce Inventory Shrinkage: A Practical Guide
Understanding Inventory Shrinkage: The Hidden Challenge in Warehousing
Inventory shrinkage is a critical issue that every warehousing operation faces, often impacting the bottom line more than we realize. It represents the frustrating gap between what your inventory system reports and the actual stock present on your shelves. This discrepancy could arise from several factors, including theft, damage, loss, or simple counting errors. Understanding the causes and implications of inventory shrinkage can help mitigate its impact and streamline your operations.
What is Inventory Shrinkage?
At its core, inventory shrinkage is the difference between the recorded inventory in your system and what is truly available. For many warehouse operators, this can lead to substantial financial losses if not addressed effectively. According to various studies, the average shrinkage rate in the retail sector can range from 1% to 2%, but in the warehousing sector, the number can sometimes climb even higher due to various operational challenges.
Causes of Inventory Shrinkage
- Theft: This is one of the most significant contributors to inventory shrinkage. Internal theft (from employees) and external theft (from customers or other intruders) can drastically impact your inventory levels. Implementing stricter security measures and cultivating a culture of trust and accountability can help mitigate this risk.
- Damage: Products that are damaged during storage, picking, or shipping often contribute to shrinkage. Reducing damage can be achieved through better staff training, improved handling processes, and investing in appropriate storage solutions.
- Loss: Sometimes, inventory can be simply misplaced. Staff may inadvertently place items in the wrong location, leading to confusion about stock levels. Regular audits and a robust labeling system can significantly reduce these mishaps.
- Counting Errors: In a busy warehouse, human error is almost inevitable. Mistakes during physical counts or data entry can lead to discrepancies between recorded and actual inventory. Incorporating technology such as barcode scanners, RFID tracking, and regular training for staff can help minimize these errors.
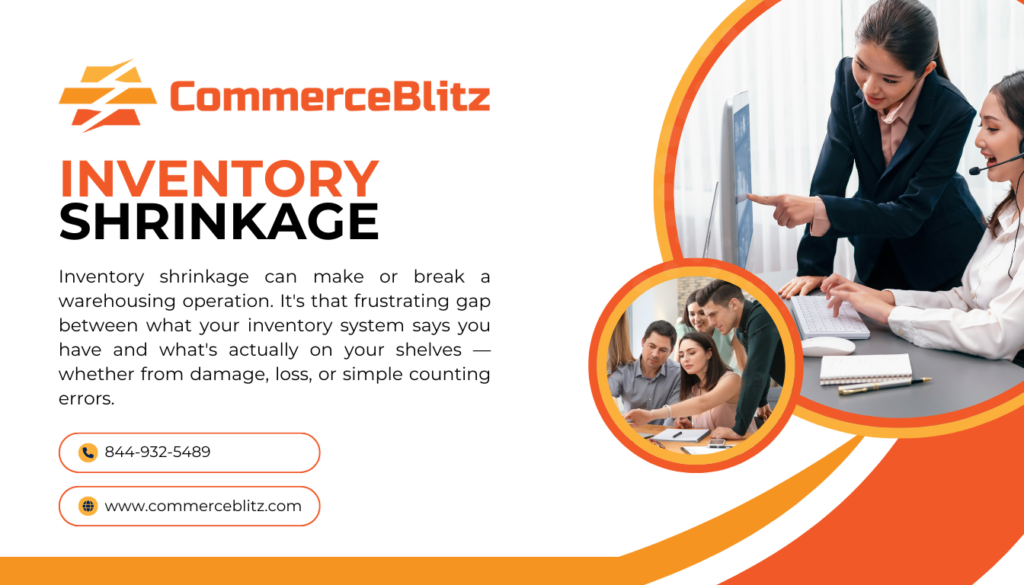
The Implications of Inventory Shrinkage
The effects of inventory shrinkage extend beyond just lost products. They can lead to:
- Financial Losses: Shrinkage directly translates to reduced revenue. Replacing missing stock not only impacts profits but also affects cash flow and budgeting.
- Operational Inefficiencies: Frequent stock discrepancies can disrupt your workflow, leading to increased labor costs as staff must spend time chasing down missing items or fixing errors.
- Customer Dissatisfaction: When inventory records are incorrect, it can lead to stockouts or overpromising on availability. This not only frustrates customers but can damage your brand’s reputation and loyalty.
Strategies to Combat Inventory Shrinkage
- Conduct Regular Audits: Periodic inventory audits can help you catch discrepancies before they become larger issues. Utilize cycle counting and full physical inventories to keep tabs on your stock.
- Enhance Security Measures: Consider implementing surveillance cameras, alarm systems, and restricted access areas to deter theft. Training employees on recognizing suspicious behavior can also be beneficial.
- Invest in Technology: Utilizing inventory management software and tracking technologies can greatly reduce human error and improve accuracy. Keeping your systems updated is key to minimizing shrinkage.
- Employee Training: Ensuring that your staff is well-trained on proper handling and inventory management techniques will foster a culture of accountability and accuracy.
In conclusion, while inventory shrinkage presents various challenges, it is manageable with the right approach. Understanding its causes and implementing targeted strategies can significantly enhance your warehousing operations, reduce financial losses, and keep your customers happy. After all, a well-organized and accurately stocked warehouse is fundamental to success in today’s competitive market.
If you’re looking for assistance to improve your inventory management practices or need tailored solutions for your warehousing operations, feel free to reach out or schedule a demo to see how CommerceBlitz OMNI can help. Together, we can tackle the challenges of inventory shrinkage head-on!